河南金伟自动化设备有限公司
专业玻璃钢拉挤模具与设备制造商,为客户提供高品质自动化设备及解决方案
河南金伟自动化设备有限公司位于中国河南省安阳市滑县白道口镇,是一家专注于玻璃钢复合材料制造领域的技术企业。致力于为客户提供高品质的自动化设备及解决方案,主要产品包括玻璃钢拉挤模具、液压拉挤设备、伺服液压牵引机、导毡器、切毡机、树脂分散机等。20年经验,服务客户超3000家,多种规格可选,价格实惠,满足各种定制需求。核心优势:· 技术创新与研发能力:公司拥有一支经验丰富、技术高超的研发团队,不断探索新技术的应用,确保产品性能始终处于行业超前地位。· 产品质量与可靠性:我们从原材料采购到成品检验,每一步都经过严格的质量控制,确保设备稳定可靠。· 定制化解决方案:我们深入了解每一位客户的具体需求,提供从设计、制造到安装调试的一站式服务,确保客户得到更合适的解决方案。· 售后服务与支持:我们建立了覆盖全国的服务网络,提供24小时快速响应服务,确保客户设备的正常运行。
-
服务客户3000
+
年
-
产品体系50
+
种
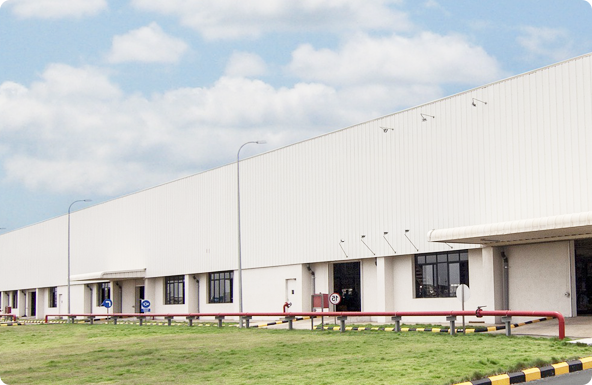
以优质的产品质量,服务于新老客户
为客户定制满意的产品,全天候、全时制、全方位提供服务
-
智能制造背景下的伺服液压拉挤设备发展趋势伺服液压拉挤设备作为复合材料连续成型领域的关键装备,其技术升级与智能制造深度融合已成为产业转型的核心驱动力。随着新能源汽车、风电叶片等领域对高性能复合材料需求的激增,传统拉挤设备在工艺精度、能耗效率及自适应控制等方面面临严峻挑战。2025年,以数字孪生、边缘计算为代表的新一代信息技术,正推动伺服液压拉挤设备向多维度智能化方向演进,构建从工艺优化到全生命周期管理的技术闭环。1. 高动态响应与智能控制伺服液压拉挤设备通过集成高精度伺服电机与智能液压系统,实现了牵引速度±0.1mm/s的闭环控制精度。例如,某航空航天碳纤维型材生产线采用基于FPGA的实时控制算法,将模具内树脂压力波动控制在±5kPa以内,制品孔隙率降低至0.3%以下。结合深度学习技术构建的工艺参数自整定系统,可在30秒内完成传统需2小时的手动调试流程,生产效率提升40%。2. 数字孪生驱动的工艺优化基于物理模型与实时数据融合的数字孪生平台,成为伺服液压拉挤设备智能化升级的核心载体。某新能源电池箱体制造商通过部署三维热-力耦合仿真系统,将模具温度场均匀性从±8℃优化至±2℃,产品固化周期缩短25%。2024年落地的5G+边缘计算解决方案,使设备数据采集频率从100Hz提升至10kHz,工艺异常检测响应时间压缩至50ms级。3. 模块化架构与能效突破采用可重构模块化设计的伺服液压拉挤设备,通过标准接口快速适配不同规格产品的生产需求。某汽车防撞梁产线通过更换模组化牵引单元,实现碳纤维/玄武岩纤维双材料产线的柔性切换,设备复用率提升60%。新型永磁同步液压泵与能量回收系统的组合,使单位能耗较传统设备降低32%,达到ISO 50001能源管理体系认证标准。在智能制造浪潮的推动下,伺服液压拉挤设备正经历从“单一执行”到“感知-决策-执行”一体化的范式变革。通过高精度伺服控制、数字孪生优化及模块化能效提升等技术创新,该设备在工艺稳定性、生产柔性及绿色制造等方面取得突破性进展。预计至2026年,融合AI大模型的第四代伺服液压拉挤设备将实现工艺自主迭代,推动复合材料制造成本再降低30%,为航空航天、轨道交通等战略领域提供核心装备支撑。这一发展路径不仅重塑了复合材料加工技术体系,更成为“双碳”目标下制造业转型升级的典型示范。2025-03-05
-
基于有限元分析的拉挤模具优化设计拉挤模具是复合材料连续成型工艺中的核心装备,其结构设计的合理性直接影响制品的尺寸精度、力学性能及生产效率。随着高性能纤维增强树脂基复合材料的广泛应用,传统经验驱动的模具设计方法已难以满足复杂截面、高精度产品的制造需求。近年来,基于有限元分析的数字化设计技术为拉挤模具的迭代优化提供了科学支撑,该方法通过精确模拟材料流动、固化反应与热力耦合过程,显著提升了模具设计的可靠性与时效性。1. 有限元模型构建与参数化分析拉挤模具的有限元分析需建立包含树脂流动通道、加热系统、型腔结构的精细化三维模型。以某T型截面碳纤维拉挤模具为例,采用HyperMesh进行网格划分时,需对模具入口收敛区、定型段等关键部位实施局部加密,确保壁面边界层的网格密度达到0.5mm,以捕捉树脂流动的剪切速率梯度。通过ANSYS Workbench平台设置非牛顿流体本构方程与固化动力学模型,可量化不同牵引速度(1-3m/min)下模具内部的压力分布与温度场演变规律。2. 多目标协同优化策略针对拉挤模具常见的出口流速不均、局部过热等问题,采用响应面法与遗传算法进行多参数优化。以某风电叶片拉挤模具为例,通过正交实验发现:当入口锥角由15°调整为12°、定型段长度从800mm增至1000mm时,制品的横向厚度偏差从2.1%降至0.7%,同时模具表面温差缩小18℃。引入拓扑优化技术对模具支撑结构进行轻量化设计,可在保证刚度前提下实现15%-20%的减重,有效降低能耗。3. 数字孪生驱动的智能验证基于物联网的在线监测系统可将实时采集的模具温度、压力数据与有限元仿真结果动态比对,构建拉挤模具的数字孪生体。某汽车防撞梁模具的优化案例显示,该技术可将传统试模次数从7-8次减少至2-3次,开发周期缩短40%以上。有限元分析技术为拉挤模具的智能化设计开辟了新路径,其通过多物理场耦合仿真与数据驱动优化,显著提升了模具的服役性能与设计效率。未来随着AI算法的深度集成,有限元分析将进一步突破传统经验壁垒,推动拉挤模具向高精度、低能耗、自适应方向演进,为航空航天、新能源等领域的复合材料构件制造提供核心装备保障。2025-03-05
-
拉挤模具精度提升与质量控制新方法研究在风电叶片、轨道交通等领域对高性能复合材料需求激增的背景下,拉挤模具作为连续成型工艺的核心装备,其精度与质量控制水平直接决定产品性能与生产成本。2024年以来,随着数字孪生、机器学习等技术的深度应用,拉挤模具在材料、工艺及检测环节实现创新突破,推动行业向高精度、低损耗方向加速转型。一、设计优化与仿真技术:突破传统精度瓶颈数字孪生预演工艺参数基于数字孪生技术构建拉挤模具三维动态模型,可模拟树脂流动、纤维分布与热应力变化,提前识别模具变形风险。某企业采用该技术后,模具调试周期缩短40%,产品尺寸偏差稳定在±0.08mm以内。拓扑优化强化结构稳定性通过有限元分析优化拉挤模具内腔流道设计,减少应力集中区域。例如,采用蜂窝支撑结构的模具可将热变形量降低30%,使用寿命延长50%。二、材料与工艺创新:构建全流程质控体系新型合金材料应用采用V10粉末合金钢替代传统Cr12MoV材料,使拉挤模具硬度提升至62HRC,耐磨性提高3倍,尤其适用于碳纤维等高磨蚀性材料成型。梯度热处理工艺针对复杂截面拉挤模具,开发“淬火+多段回火”工艺,将残余应力控制在15MPa以下,避免加工后开裂风险45。在线监测与动态补偿集成高精度传感器实时采集模具温度、压力数据,通过PID算法自动调节加热速率,使树脂固化均匀性提升25%,废品率降至1.2%以下。三、智能检测与闭环管理:实现零缺陷生产机器视觉缺陷识别在拉挤模具出口部署工业相机,利用深度学习算法自动检测产品表面气泡、缺胶等缺陷,检测精度达99.7%,较人工检测效率提升10倍。数据驱动的预测性维护基于历史数据建立模具磨损寿命模型,提前预警关键部件失效风险。某工厂应用后,模具非计划停机时间减少60%,维护成本下降35%。拉挤模具的精度提升与质量控制新方法,通过设计仿真、材料革新与智能检测技术的融合,显著提升了复合材料制品的性能与生产效益。2025年,随着量子传感、自适应控制等技术的成熟,拉挤模具将实现纳米级精度调控与零废料生产,为高端制造业提供更高效、绿色的解决方案。
-
探索伺服液压拉挤设备的高精度控制技术随着航空航天、新能源汽车等领域对高性能复合材料需求的激增,伺服液压拉挤设备的精密控制技术成为行业升级的核心课题。传统液压设备因响应滞后、精度不足等问题,难以满足复杂截面的连续成型需求。近年来,基于多轴协同控制、智能算法与数字孪生技术的融合应用,伺服液压拉挤设备在精度、效率与稳定性方面实现了跨越式发展。一、高精度控制的核心原理伺服液压拉挤设备的控制体系以闭环反馈为核心,通过多层级协同实现精准调控。多轴同步控制:设备通过伺服电机驱动液压泵,结合高分辨率编码器实时反馈拉挤速度与位置,确保纤维增强材料在模具内的均匀分布。例如,南京埃斯顿公司的双液压轴控制器Flexcon可实现±0.05mm的定位精度,显著提升产品一致性。动态压力补偿:液压系统采用比例阀与压力传感器联动,实时调整油缸输出力,抵消材料固化过程中的黏度变化,避免因压力波动导致的产品缺陷。智能温控技术:模具内集成温度传感器与PID算法,精确调控加热/冷却速率,确保树脂在最佳条件下固化,减少内应力形变。二、技术创新的关键突破当前技术革新聚焦于智能化与集成化方向:数字孪生优化:通过虚拟仿真模型预演工艺参数,缩短调试周期并优化能耗。例如,某企业利用实时数据映射技术,将设备调试效率提升40%以上。边缘计算赋能:在控制器中嵌入边缘计算模块,实现毫秒级响应。2024年推出的新一代PLC系统,可同时处理32路信号,支持复杂工艺的多变量自适应控制。安全冗余设计:集成Pilz安全模块,通过光栅、急停等多重防护机制,确保设备在高速运行下的安全性,故障率降低至0.01‰以下.三、行业应用与效益高精度控制技术已成功应用于风电叶片、碳纤维型材等领域。以某1600kN液压机为例,采用伺服液压系统后,其生产节拍缩短15%,良品率从92%提升至98%,能耗降低20%。此外,在半导体封装材料等高附加值领域,设备可支持0.1μm级微结构成型,推动行业向精密化发展。伺服液压拉挤设备的高精度控制技术,通过机电液一体化设计与智能化升级,解决了复合材料成型中的精度与效率瓶颈。未来,随着5G通信、AI预测性维护等技术的深度应用,设备将进一步向自适应、低能耗方向演进,为高端制造业提供更强大的技术支撑13。这一领域的持续突破,不仅推动复合材料工艺革新,更将加速工业4.0时代的精密制造进程。
-
智能化拉挤模具:让复合材料生产更“聪明”拉挤模具就像制作面条的模具,但它的“面条”是玻璃钢、碳纤维这些高强度材料。过去这类模具只能按固定模式工作,而现在装上“智慧大脑”后,生产效率提高40%、废品率降到0.5%以下56。2025年全球60%的轨道交通、风电叶片企业都用上了这种智能模具,它正让复合材料生产变得更精准、更省力。一、技术升级三大看点1. 拉挤模具模具自己会“看病”装上了温度传感器和压力探头,能实时监控树脂是否涂匀、纤维有没有打结发现产品有0.1mm的裂纹,自动启动激光修补,比老师傅修得更快更准2. 生产速度“自由切换”遇到厚壁管材自动降速15%,薄壁型材提速到2米/分钟,就像汽车自动换挡某企业改造后,风电叶片主梁的生产周期从3天缩短到36小时3. 手机就能管工厂通过工业互联网,在办公室就能看到模具运行状态,还能远程调整参数系统自动记录10万组生产数据,新手也能一键调出最佳配方二、企业省钱三笔账1. 电费省一半新型液压系统待机功耗降低80%,一年省下1.5万度电,够30个家庭用一年2. 材料不浪费智能控制系统让树脂利用率达到98%,每生产1吨产品少浪费200公斤原料3. 拉挤模具模具更耐用自清洁刮刀让模具连续工作10天不卡料,寿命延长2倍,维护费省40%2026年的拉挤模具将更“懂人心”——工人戴AR眼镜修模具,眼前自动显示故障解决方案;模具能根据订单自动切换生产模式,从造风电叶片转产汽车保险杠只需15分钟。这种“会思考”的模具,正在把传统工厂变成24小时运转的“黑灯工厂”,让中国制造在全球竞争中跑出加速度。
-
伺服液压牵引机节能技术创新:驱动绿色制造的精密内核在“双碳”目标驱动下,工业装备的节能技术迭代成为制造业转型升级的核心议题。伺服液压牵引机作为精密传动领域的核心设备,其能耗占生产总成本的30%以上13。近年来,通过伺服驱动、泵控技术、能量回收系统等创新方案,该设备的能效比已提升至传统机型的2-3倍45,形成了兼具经济性与环保价值的解决方案。一、核心技术突破:从异步电机到伺服驱动的能效跃迁传统液压牵引机依赖异步电机驱动定量泵,空载时通过溢流阀泄压维持系统压力,造成30%-60%的无效能耗27。伺服液压牵引机采用永磁同步电机与变量泵的直驱架构,通过实时压力-流量反馈闭环控制,实现“按需供能”。例如在牵引机空载阶段,伺服电机可完全停机,消除待机能耗;在负载变化时,电机转速精确匹配执行机构需求,避免溢流损失35。实测数据显示,某金属板材加工企业的200吨级伺服牵引机年度节电量达1.2万度,综合节能率突破65%23。二、泵控技术重构:从阀控冗余到精准匹配的进化路径突破传统阀控系统的能量损耗瓶颈,新型伺服牵引机采用泵控技术替代多级阀组。通过高精度伺服电机直接驱动轴向柱塞变量泵,将压力-流量控制单元集成于泵体内部,减少管路压力损失40%以上34。该技术结合数字孪生系统,可预判牵引工艺曲线,动态调整泵排量。例如在牵引机加速阶段,泵排量提升至额定值的150%;减速阶段则切换至能量再生模式,将制动动能转化为电能回馈直流母线37。这一设计使系统发热量降低50%,冷却装置功耗下降70%58。三、能量回收系统的智能化升级2024年落地的第三代伺服牵引机引入超级电容-锂电池混合储能单元,实现多工况能量回收。在牵引机构制动阶段,伺服电机转换为发电机模式,捕获的动能经双向变流器储存于储能模块;在峰值负载时,储能单元与电网协同供电,降低变压器容量需求30%37。某汽车底盘件生产企业采用该方案后,单台设备年减少碳排放12吨,电网冲击电流抑制效果达90%58。伺服液压牵引机的节能创新已从单一部件优化转向系统级能效重构。随着数字孪生、边缘计算等技术的深度融入,2025年该领域有望实现全生命周期能耗可视化管控,推动单位产值能耗下降至0.8kW·h/吨以下37。这种技术范式不仅重塑了液压传动的效率边界,更为工业装备的绿色化转型提供了可复用的技术模板。
-
173-3906-7777
-
130-8385-3711
-
微信公众号